An Extensive List for Effective Welding Inspection Practices
In the realm of welding, the integrity of structures is vital, requiring an extensive method to assessment methods. A detailed list acts as a crucial tool in making sure adherence to market requirements, including vital pre-welding, in-process, and post-welding assessments. By systematically dealing with material confirmation, weld top quality, and detailed documents, organizations can substantially improve safety and efficiency. Nonetheless, what certain aspects should be prioritized in each stage to attain ideal results? Discovering these important elements can yield understandings that exceptionally impact welding procedures.
Recognizing Welding Specifications
Welding standards play a critical function in making certain the high quality and safety of welded frameworks and elements. These criteria establish the requirements for materials, procedures, screening, and evaluation, therefore offering a structure for consistent quality control in welding processes. Different companies, including the American Welding Culture (AWS), the International Company for Standardization (ISO), and the American Society of Mechanical Designers (ASME), have actually developed comprehensive criteria that control various facets of welding.
Comprehending welding standards is necessary for professionals in the field, as adherence to these standards decreases the risk of flaws and failings in bonded joints. These standards cover certain needs for weld top quality, including acceptable resistances, the kind of welding techniques to be used, and the certifications required for welders and assessors.
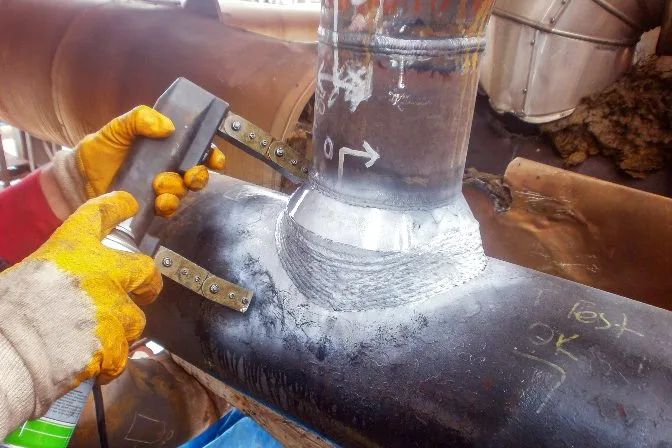
Pre-Welding Inspection Actions
Before any type of welding process begins, a comprehensive pre-welding inspection is important to identify possible issues that might compromise the high quality of the weld. This initial step acts as a vital structure for guaranteeing conformity with appropriate welding codes and criteria.
The first action in the pre-welding inspection is to confirm the products being used. This includes monitoring for the proper type and quality of steels as specified in the job documents. Next off, it is essential to check the fit-up of the parts to guarantee appropriate placement and joint configuration. Misalignment can cause poor penetration and structural weaknesses.
Additionally, evaluating the sanitation of the surfaces is vital; pollutants such as paint, corrosion, or oil can negatively impact the top quality of the weld. Following this, a comprehensive assessment of the welding equipment ought to be carried out, making sure that it is calibrated and in great working condition.
Last but not least, examining the certifications of the welding workers is critical. Welders must have the essential certifications and experience to execute the details welds needed for the task. By sticking to these pre-welding evaluation steps, the chance of flaws and failings in the final weld can be considerably reduced.

In-Process Inspection Strategies
In-process inspection methods play a vital function in ensuring the stability and top quality of welds as they are being performed. These strategies allow examiners to recognize defects or variances from requirements in real time, consequently guaranteeing and protecting against costly repair work adherence to style needs.
One key technique includes aesthetic examination, where inspectors evaluate the weld bead for harmony, infiltration, and correct account. This can be complemented by the use evaluates to determine weld measurements, making certain conformity with fixed resistances. Additionally, the application of non-destructive screening (NDT) techniques, such as ultrasonic screening or magnetic fragment screening, throughout the welding procedure can disclose subsurface imperfections that might not be noticeable on the surface.
An additional vital facet is monitoring welding parameters, including voltage, amperage, and travel speed. Uniformity in these criteria is critical for achieving optimum weld top quality. Recording these criteria throughout the welding operation offers a traceable record for future referral.
Educating employees in appropriate evaluation methods and making use of appropriate devices enhances the efficiency of in-process assessments. By integrating these practices, organizations can attain higher top quality welds, lower rework, and inevitably make sure the security and dependability of welded frameworks.
Post-Welding High Quality Checks
Following the conclusion of welding procedures, post-welding quality checks are crucial to validate that the welds satisfy all specified standards and needs. These checks are important for making sure the integrity and durability of the bonded joints. The evaluation procedure usually begins with an aesthetic examination, analyzing for surface issues such as fractures, porosity, or incomplete combination.
Subsequently, non-destructive screening (NDT) methods, such as ultrasonic testing, radiographic screening, or magnetic bit screening, may be used to discover inner defects that are not noticeable to the naked eye. Each technique has its unique benefits and is picked based on the weld's place, material type, and the nature of the application.
In addition, verifying dimensional precision is an important element of post-welding top quality checks. This involves determining the weld's placement, profile, and size to make sure conformity with design specs. Evaluating the mechanical residential properties of the weld, consisting of tensile toughness and ductility, can provide further assurance of performance under operational conditions. Generally, complete post-welding examinations are vital for maintaining adherence, safety, and performance to regulatory and sector criteria.
Documentation and Coverage
Exactly how can effective documents and reporting enhance the welding examination process? Accurate paperwork and comprehensive coverage are vital elements that ensure the honesty and quality of welding procedures. Welding Inspection Milwaukee. They work as an official document of assessment searchings for, promoting accountability and traceability in conformity with industry requirements

A well-structured reporting system allows inspectors to clearly interact any kind of non-conformances, locations, or disparities calling for renovation. This transparency fosters an atmosphere of constant renovation, as stakeholders can conveniently assess past performance and carry out rehabilitative activities.
In addition, effective documentation includes comprehensive records such as welding procedure specs (WPS), go to my site welder certifications, and assessment lists. These components give a structure for reviewing weld top quality and adherence to developed standards. In case of disagreements or top quality concerns, weblink detailed documents offers as a reliable referral, lowering obscurity and shielding all events included.
Finally, preserving organized documents aids in training and licensing workers, guaranteeing that industry best techniques are maintained. Eventually, precise documentation and reporting not just boost the welding assessment process yet additionally contribute to the overall safety and security and integrity of welded structures.
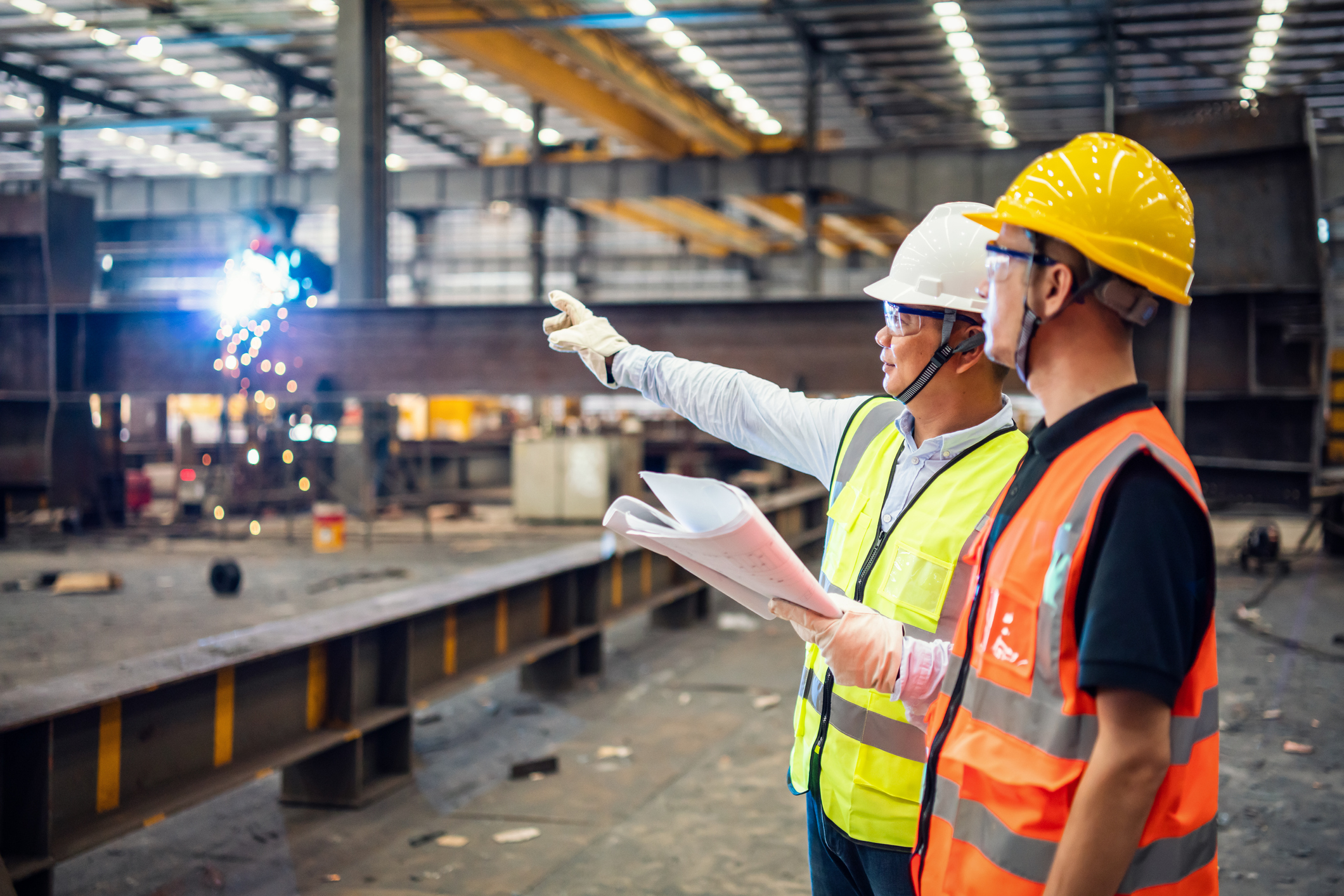
Final Thought
In verdict, a comprehensive checklist for reliable welding inspection techniques is vital for making certain top quality and safety and security in bonded frameworks. Adherence to established welding requirements, precise pre-welding evaluations, rigorous in-process evaluations, and comprehensive post-welding quality checks collectively add to the honesty of bonded joints.
Welding requirements play an important role in ensuring the top quality and safety and security of bonded structures and components. Various organizations, consisting of the American Welding Society (AWS), the International Organization for Standardization (ISO), and the American Culture of Mechanical Designers (ASME), have created detailed requirements that govern various elements of welding.
Following the conclusion of welding operations, post-welding quality checks are essential to verify that the welds meet all defined requirements and requirements - description Welding Inspection Milwaukee.In verdict, a detailed checklist for reliable welding evaluation techniques is important for ensuring top quality and safety in bonded structures. Adherence to developed welding standards, careful pre-welding evaluations, strenuous in-process assessments, and detailed post-welding high quality checks jointly contribute to the stability of bonded joints